During the COVID-19 pandemic, Pinnacle Precision supplied a local medical manufacturer with precision metal parts and assemblies to support delivery of life-saving ventilators.
The heroes of the COVID-19 shut down were the ones that kept us all healthy, safe, fed, educated, and entertained. Our gratitude is limitless for these people.
There were behind-the-scenes heroes as well, like the team at Pinnacle Precision Sheet Metal, Inc. in Anaheim, California, who worked hand-in-hand with a local medical manufacturer, who were building ventilators for hospitals and clinics around the United States.
“It was an honor to be part of helping people through those hard times,” says Pinnacle’s Plant Manager, Steve Jacques. “Our team took great pride in pulling together during the pandemic and saving lives.”
Pre-pandemic, Pinnacle’s team delivered around 30 units a quarter of precision sheet metal parts and assemblies to be used in ventilators. At the height of the COVID-19 pandemic, Pinnacle increased its production of these critical components by more than 15x to more than 500 units per quarter. Since the beginning of 2020, over 3,000 units have been made and shipped to a local medical manufacturing partner.
“We moved as fast as possible to support a very aggressive timeline and delivery schedule,” reports Jon Weir, Pinnacle’s Customer Service Manager. “From the initial purchase order to first delivery was three weeks.”
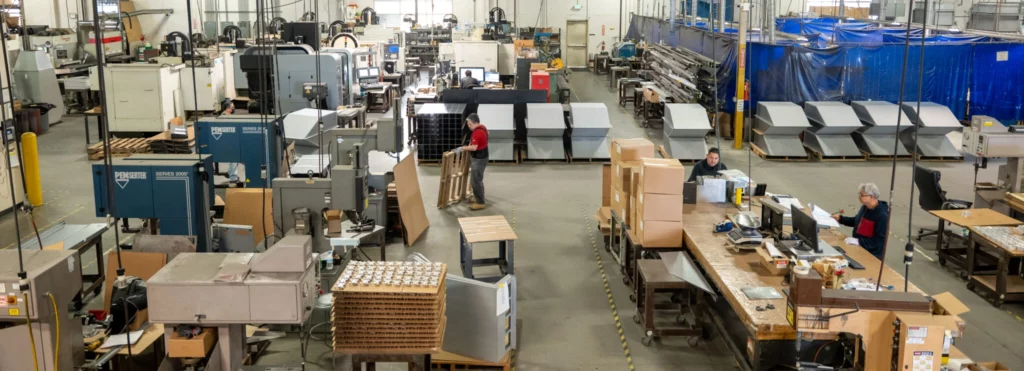
Kicking production into high gear took an all-hands-on-deck mentality, which was nothing new for Pinnacle. Since the company’s earliest days, each department has worked together to ensure accurate, durable, and precise parts are delivered on time and within budget.
The first point of contact for every project that comes through Pinnacle is the company’s Customer Service team, who works hand in hand with customers to understand technical, material, and application requirements.
During the pandemic, Jon Weir and Pinnacle’s Customer Service crew constantly communicated with our partner’s engineering and production staff to ensure the metal parts, components, and assemblies arrived precisely when needed.
The demands of Class A parts — and the tight delivery deadlines — meant that Pinnacle’s Technical, Production, and Finishing teams needed a seamless production schedule with maximum accuracy and dependability.
“We have decades of experience on our production floor, and we know how to work together,” Jacques says. “We meet every morning to discuss the day and see where people need help. Those meetings were crucial during this work because we knew how important each day was and how many people we were helping.”
A local medical manufacturer turned to Pinnacle’s Assembly team to begin building its 3100A/B HFOV ventilators. Led by Jacques and the company’s assembly professionals, each shipped piece included hardware, components, and seals that helped the manufacturing company deliver these life-saving products.
“We didn’t shut down once during the entire pandemic,” Weir points out. “We knew how important every day was, and we worked as hard as we could as a team to deliver. I’m so proud of us all.”