Of all the ways to fabricate metal parts, photochemical etching stands out for its ability to produce precise, durable, reliable, and cost-effective thin metal parts and components.
Photochemical etching is a process that circumvents traditional machining methods to produce more durable, long-lasting products with a greater degree of accuracy. It’s a highly versatile technology that produces metal parts with intricate geometries to tight tolerances.
Five of The Partner Companies’ ten specialty manufacturing centers specialize in photochemical etching (PCE), also known as photochemical machining or chemical blanking. The centers are across the United States, from California to Massachusetts. Each stays on top of the latest PCE manufacturing innovations, striving to improve its standards of excellence while maintaining a partner-first mentality.
What is Photochemical Etching
Photochemical etching is a leading processing method to produce thin metal parts used in thousands of end products that save lives, help us communicate, and drive innovation.
PCE is a subtractive process where corrosive chemicals etch a desired shape or pattern into the manufacturer’s metal of choice. After selecting and washing the material to remove oils and contaminants, PCE operators laminate the metal sheet with a UV-sensitive dry film photoresist. The photoresist acts as a barrier between the metal and the chemical etchants.
A UV laser digital imaging tool transfers an image of the desired part to the metal sheet, and then that image is developed, which removes the exposed resist.
That metal sheet then travels to an etching machine, which sprays a chemical etchant onto the metal, subtracting material not protected by the photoresist.
From there, the sheet is rinsed and inspected for imperfections that could compromise the part’s integrity.
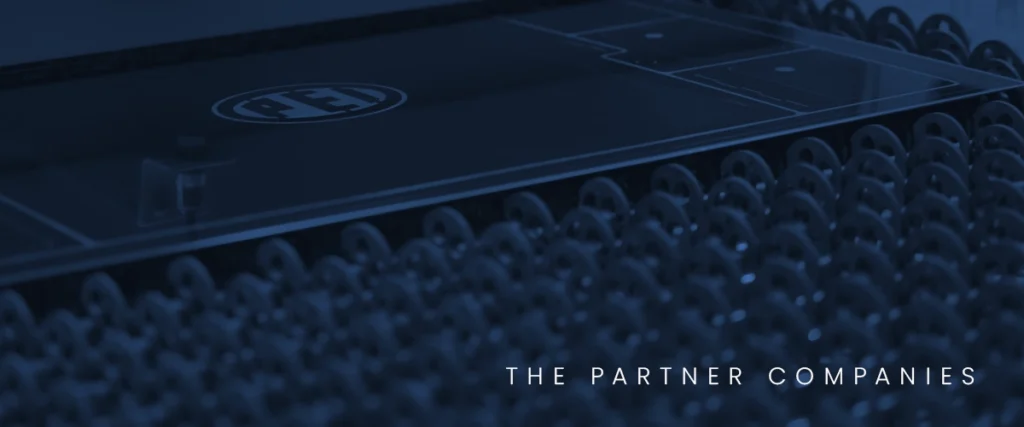
The Advantages Of PCE
There are many benefits to producing thin metal parts via photochemical etching, including:
Fast Turnaround & Production Times
The digital nature of photochemical etching part designs allows for faster production of prototypes and production-quality pieces. Even if a customer requests changes to the part design, design engineers can easily modify it using computer software without needing new tooling.
Because the photochemical etching process begins on a computer, parts can be produced more quickly, with no retooling costs or delays if a change is required.
Further, PCE enables the production of multiple parts on one sheet of metal, making it a more efficient and effective way of fabricating hundreds of parts an hour.
Cost-Effective Production
Compared to mechanical machining manufacturing, digitally drawn designs and chemical etchants result in lower tooling costs throughout production. Phototools are quick to make and can last the part’s lifespan (if not longer). The process’s reproducibility enables larger production runs at reduced prices.
Because photochemical etching uses chemical etchants and digitally produced designs to create a final item, tooling costs are lower than mechanical machining operations. Furthermore, the technique may handle part designs with increased complexity or tighter tolerances without growing production costs.
Enables Production of Complex Designs
PCE is a precise subtractive process, and chemical etching does not affect metal’s inherent strength and durability compared to other conventional machining processes like stamping or laser cutting.
That fact enables operators to produce precise, uniform parts with fine details and complex geometries to tight tolerances.
Minimal Surface Burring
Photochemical etching creates products with low surface burring, eliminating the need for additional finishing procedures.
Burrs are unattractive and counterproductive flaws in metal fabrication. They typically resemble pronounced ridges, rough edges, or tiny, solid, bubble-like forms along the metal edges. The most commonly damaged material is sheet metal.
TPC’s Photochemical Etchers
TPC’s specialty manufacturing centers with photochemical etching expertise are Photofabrication Engineering, Inc. (PEI), E-Fab, Elcon, Fotofab, and Microphoto. The companies serve industry leaders in various industries, including renewable energy, defense, aerospace, medical, communications, and semiconductors.
We invite you to learn more about each company and reach out to ask how photochemically etching can help you achieve your manufacturing goals.
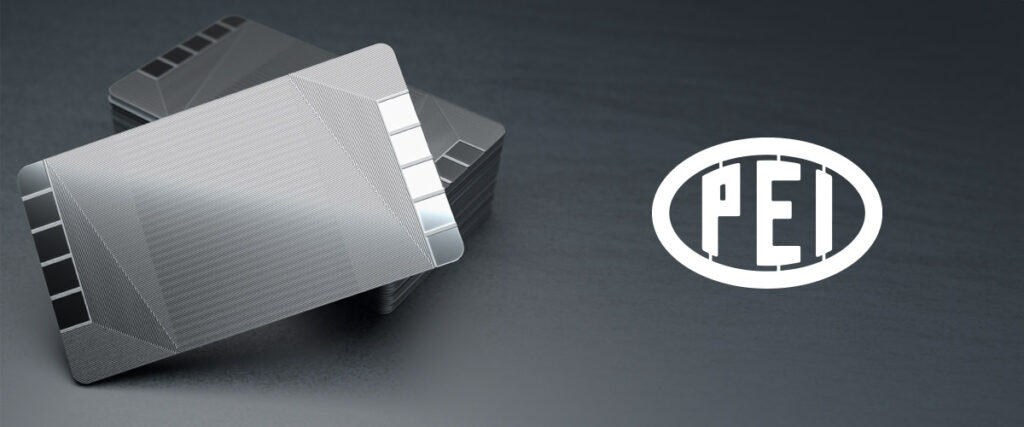
Photofabrication Engineering, Inc. (PEI)
PEI opened its doors in Holliston, Massachusets, with a modest, 4,000-square-foot building in 1968. Today, the company is the world leader in the photochemical etching of titanium and one of the largest suppliers of titanium bipolar electrolyzer plates used for hydrogen energy production. Beyond renewable energy, PEI also works with clients in the medical, aerospace, and defense sectors.
In 1983, PEI moved to a new 40,000-square-foot facility in Milford, Massachusetts, to expand its ability to serve more clients and produce larger-volume jobs. In addition to bipolar electrolyzer plates, PEI produces EMI/RF shields, microchannel plates, lead frames, encoder discs, screens, and step and flat lids, among other things.
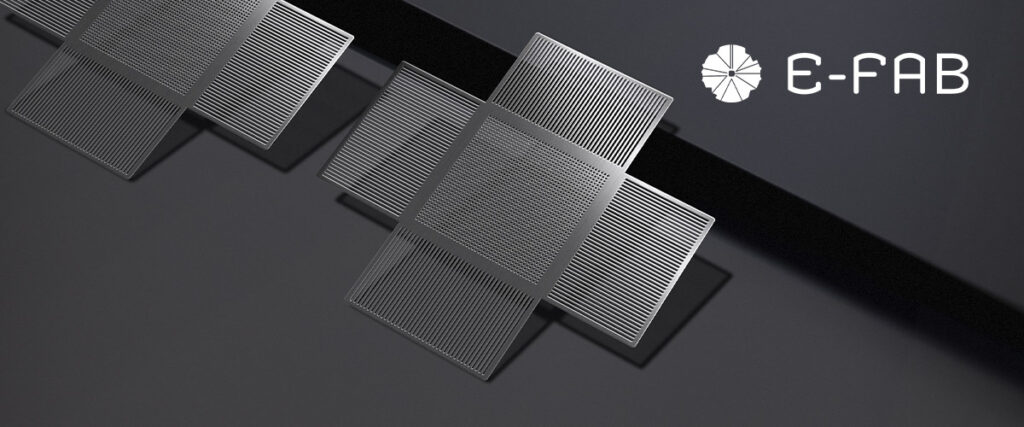
E-Fab
Since Jerry Banks and Bill Scales launched E-Fab in the heart of Silicon Valley in 1982, the company’s engineers, manufacturers, and quality assurance professionals quickly adopted the mantra, “Bring us a challenge. We’ll solve it.”
E-Fab’s team proves that daily by delivering precise, durable, and innovative solutions for the most demanding applications. Their clients include telecommunications, defense, medical, and electronics customers.
Based in Santa Clara, California, E-Fab produces a wide array of products through photochemical etching, including optical apertures, heat exchanger plates, RF shields, lids & carriers, and aerospace components, including EMI/RFI shielding, wire mesh and stabilization shims, covers, lids, and heat sinks.
E-Fab works with several important materials, including titanium, beryllium copper, stainless steel, molybdenum, Kovar, and tungsten.
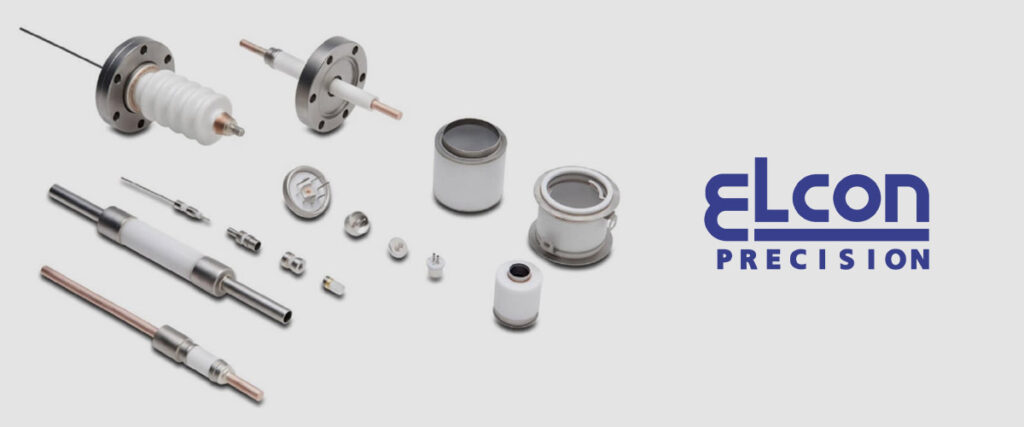
Elcon Precision
For more than 50 years, San Jose, California-based Elcon Precision has manufactured the industry’s highest-quality precision components and assemblies, serving long-standing clients in aerospace, energy, medical, defense, and space flight.
Among the parts they produce are surgical devices, semiconductors, analytical instruments, custom meshes and screens, fuel cells, and electrolyzers. Elcon’s operators are experts in brazed assembly and ceramic metallization services.
Three decades ago, Elcon invented the process of etching and forming 3D grids. Today, the company specializes in manufacturing control grids for traveling wave tubes (TWTs). TWTs are microwave amplifiers that use hemispherical grids to control and focus electron beams. Microwave receivers, communication satellites, and radar include TWTs.
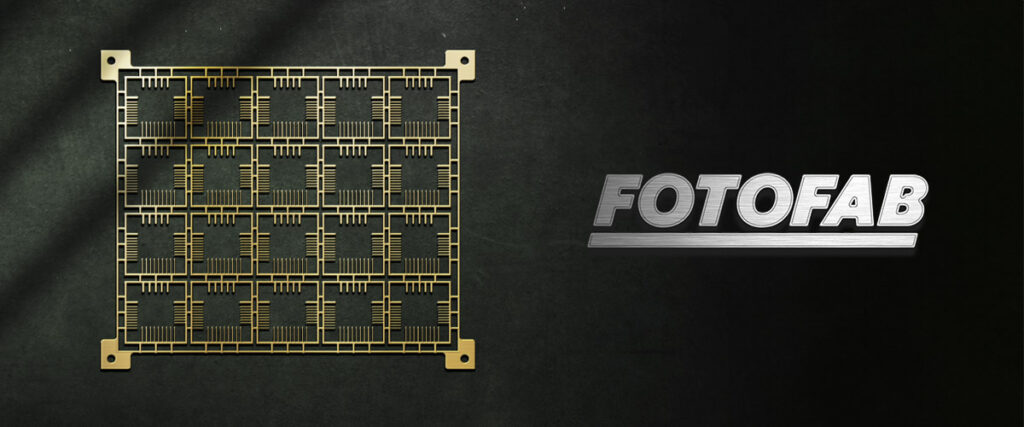
Fotofab
Fotofab opened its doors in 1967, during the early days of photochemical etching. The company works with leading medical, industrial, aerospace, and defense manufacturers from its headquarters in Chicago, Illinois.
Renowned for its rapid prototyping, large production runs, and quick turnarounds, Fotofab specializes in designing and producing custom metal fabricated components in traditional and exotic metals.
Fotofab regularly produces products, including EMI and RFI shields, encoders, flat springs, fuel cell plates, screens, step lids, and custom parts.
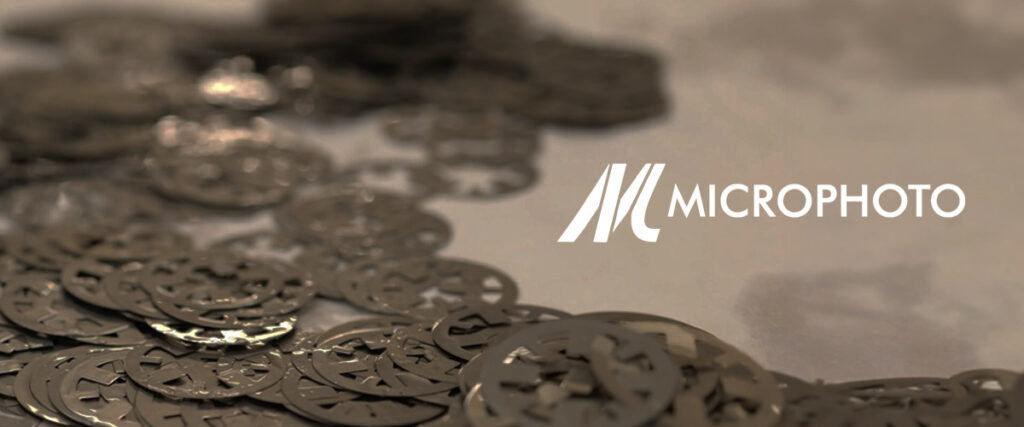
Microphoto
Microphoto opened its doors in Detroit in 1965 and is now one of the industry’s foremost experts in photochemical machining. In addition to PCM services, Microphoto provides in-house machining, forming, and stamping services to offer its customers full-service turnkey solutions.
Components produced at Microphoto include board-level shielding, electrical contacts, EMI and RFI shielding, encoders, and finger-stock gaskets.
Now located in Rosewood, Michigan, Microphoto’s customer base has expanded and diversified over the last six decades to include clients in the aerospace, automotive, decorative, defense, electronic, and medical markets. Well-known customers include Stryker Instruments, Lockheed, Boston Scientific, Pfizer, Woodward Governor, Caterpillar Inc., and L3 Technologies.
Collective strength
TPC offers its customers a consortium with rich and varied precision manufacturing expertise, including these five advanced centers specializing in photochemical etching.
With TPC’s support, each photochemical etching center leverages the power of advanced machinery to produce the parts needed across the world. Further, each center uses the latest CAD, CNC, and ERP technology and is committed to eco-friendly manufacturing processes and responsible chemical storage and processing.
All members of The Partner Companies adhere to stringent requirements to meet specific certifications, including ITAR (International Traffic in Arms Regulations), ISO 9001, AS9100, RoHS, and NIST (National Institute of Standards and Technology). TPC’s clients experience strict quality and assurance controls to ensure every thin metal part is delivered and ready for use.
TPC stands ready to find a solution to your most pressing needs. Contact us to learn how we can help.