Fotofab delivers custom high-precision thin metal components with value-added services to prominent industry leaders.
Located in the northwestern section of Chicago, IL, only four miles from the famed Wrigley Field, Fotofab has a rich and illustrious history as an outstanding provider of precision thin metal fabrication services.
Founded in 1967, Fotofab quickly established itself as a reliable and innovative client partner. It has continually invested in state-of-the-art equipment to service industries ranging from aerospace and defense to electronics and medical devices. Fotofab consistently delivers the highest quality products using the latest digital technology to manufacture custom metal products.
Fotofab’s skilled engineers and technicians collaborate closely with customers to understand their unique requirements and provide custom tailored solutions. They focus on high-quality, cost-efficient products, value-added services (including forming, plating, stamping, diffusion bonding, and finishing), and individualized customer support.
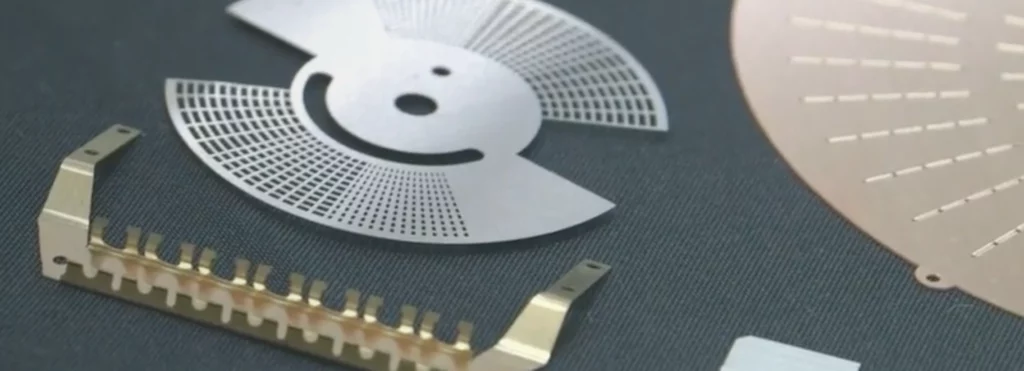
A Storied History Of Innovation and Leadership
Metal etching dates back to the Middle Ages when soldiers decorated their armor before battle. Since then, blacksmiths, silversmiths, fabricators, artists, and scientists manually etched metal to create horseshoes, printing plates, rocket parts, and thousands of other essential components.
In the early 1900s, The Buckbee Mears Corporation introduced a new etching metal method that inspired generations of engineers and manufacturers to design complex parts used in several industries. Kodak, then a legendary place for innovation, expanded the art and science of photochemical etching during the 1960s.
Kodak began offering seminars in this new manufacturing process, in part to boost the sales of the company’s film and photoresist (an essential part of the photochemical etching process) products.
Fotofab’s founder, Howard Friedman, attended one of those seminars. Inspired, he launched Fotofabrication Corporation in 1967.
The company took on the challenge of perfecting the process explained by Kodak, pioneering chemical etching, an advanced manufacturing technique that allows for the precise fabrication of intricate metal components. This breakthrough technology enabled the company to offer high-quality parts with unparalleled accuracy and consistency.
Over the past 56 years, Fotofab’s engineers and manufacturers perfected the process and have folded in several high-precision thin metal fabricating and forming services to offer turnkey solutions.
Today, Fotofab delivers quick-turn prototype projects and high-volume production runs. Customers can progress from ideation to prototype in as little as 24 hours, and Fotofab can etch over 50 different metal alloys, including aluminum, titanium, elgiloy, and copper alloys.
Charles Cohen, President of Fotofab, offers a glimpse into the company’s customer-centric approach. With a sense of pride, he emphasizes their commitment to collaboration, stating, “We take pride in working with our customers in developing prototypes and production parts.” For Fotofab, one of their key advantages lies in their remarkable manufacturing speed—an asset they leverage to the fullest extent. Cohen’s sentiment rings true as he shares, “It is our joy when we exceed our customers’ very tight timelines.” This dedication to exceeding expectations showcases Fotofab’s unwavering commitment to their clients and their relentless pursuit of excellence in every project they take on.
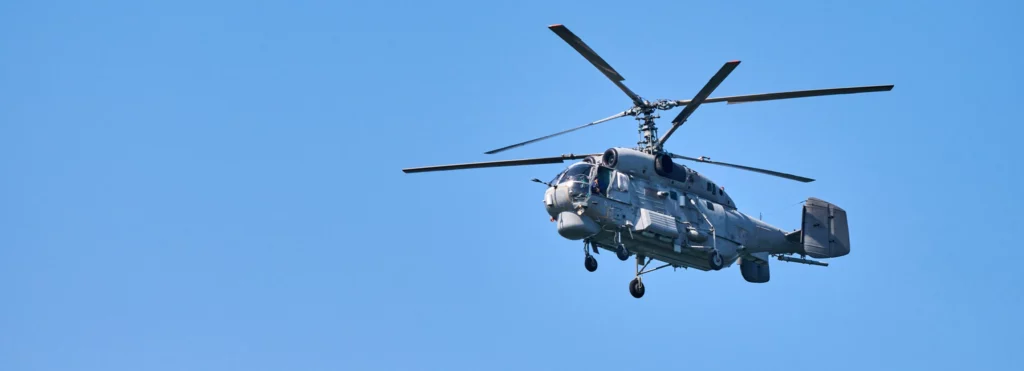
Serving the World’s Most Important Industries
Fotofab serves leading manufacturers across several industries, including aerospace and defense, medical, energy, industrial, electronics, optics, and telecommunications. The company operates as a one-stop resource to its customers and offers complete traceability from concept to production.
The company regularly produces essential parts and components, including:
Aerospace & Defense
Components for microwave antennas, drones, avionics, GPS systems, radar circuitry, remote monitoring and control systems, and board-level EMI/RFI shields.
Medical
Stents, pacemakers, neurotransmitters, and implants for dental, structural cardiac, spinal, ophthalmic, and orthopedic components.
Industrial
Name and identification plates, flat springs, shielding, optical encoders, and short-run fabrication of obsolete metal replacement parts.
Electronics
Formed metal enclosures for hybrid electronic circuits, UHF/Microwave antennas, lead frames, inserts for injection molding, and fuse links and busbars
Optics, Photonics, and Telecommunications
Equipment faceplates, light diffusion screens, EMI shielding gaskets, optical encoders, guides, and components for communications networks.
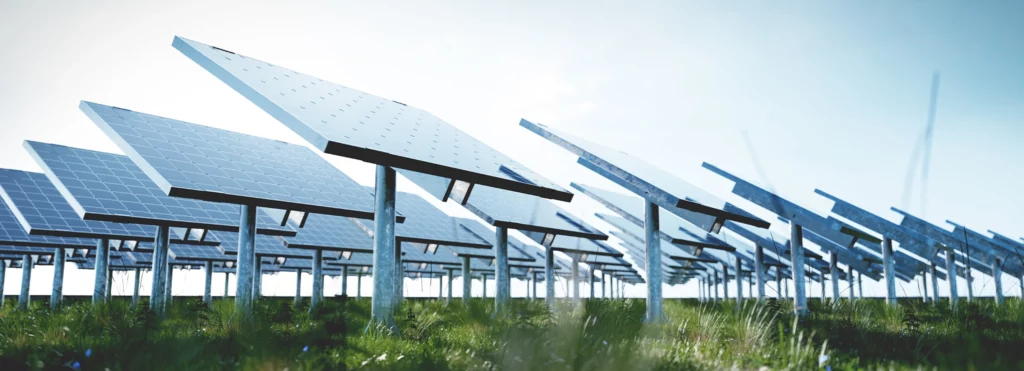
Etching For The Energy Industry
Precision thin metal parts and components with intricate geometries and tight tolerances are essential for companies working in the energy industry. Fotofab works with companies in fuel extraction, manufacturing, refining, and distribution from the petroleum, gas, electrical, coal, nuclear, and renewable energy sectors.
Fotofab delivers custom photochemically etched parts used in electric vehicles, including on-board charging (OBC) components, electric power control units (EPCU), inverters, low voltage DC-DC converters (LDC), and precision metal parts for the overall vehicle control unit (VCU).
The company takes pride in supporting the latest engineering developments within the energy sector.
Certifications and Registrations
Fotofab is AS9100D and ISO9001:2015 certified and ITAR registered.
The company has secured certification to the United States and Canada’s Joint Certification Program, produces RoHS3 and REACH-compliant parts, and is a proud, officially registered U.S. Government Vendor.
Joining The Partner Companies
Fotofab became The Partner Companies’ first manufacturing center after its purchase in 1997.
Visit the Fotofab website and contact them for more information.