TPC’s manufacturing centers utilize design for manufacturability and deliver cost and time-efficiency to benefit our customers.
The Partner Companies assembled a network of specialty manufacturers dedicated to delivering precise, reliable, durable, and high-quality solutions to leading companies in the energy, defense, medical, aerospace, and technology industries.
TPC’s manufacturers produce thin metal parts, components, complex plastic parts, assemblies, and optics via photochemical etching, injection molding, electroforming, silicon and germanium growth, electroplating, and other capabilities.
Each of TPC’s companies delivers high-touch, expert client experiences to their customers while adapting to the changing demands of each project, from rapid prototypes to high-volume runs.
Key to providing that level of service, along with the goals of cost containment, sustainability, on-time delivery, and high-quality production, is the concept of Design for Manufacturability (DFM). The continued implementation of DFM across all of TPC’s manufacturing companies has been significant and important.
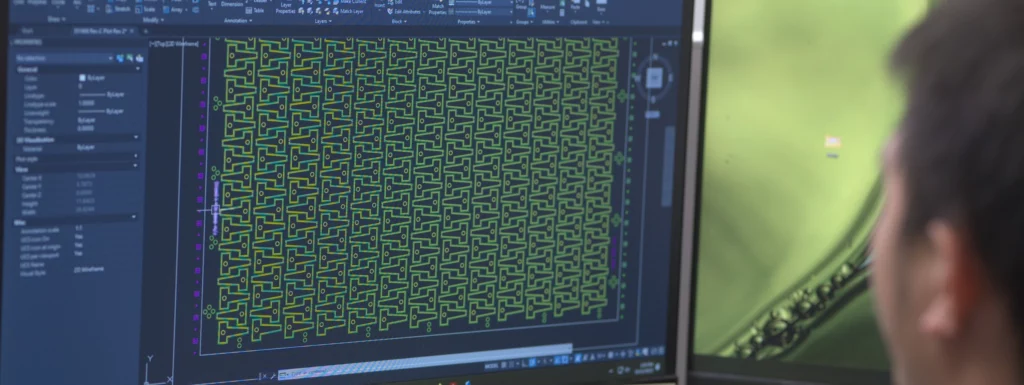
What is Design for Manufacturability (DFM)?
In essence, Design For Manufacturability (DFM) is a concept that focuses on creating and designing parts efficiently and cost-effectively. In other words, quality and quantity can go hand-in-hand as the R&D department and manufacturing engineers join forces and sync up their common goals without leaving the other in the dark. The two teams can better understand how their roles in the production process affect the final output.
DFM encourages better communication and collaboration between design and manufacturing teams, leading to more innovative and feasible designs. It is an essential component of TPC’s manufacturing centers, which constantly strive for newer and better ways to improve parts production without sacrificing the quality and integrity they are known for.
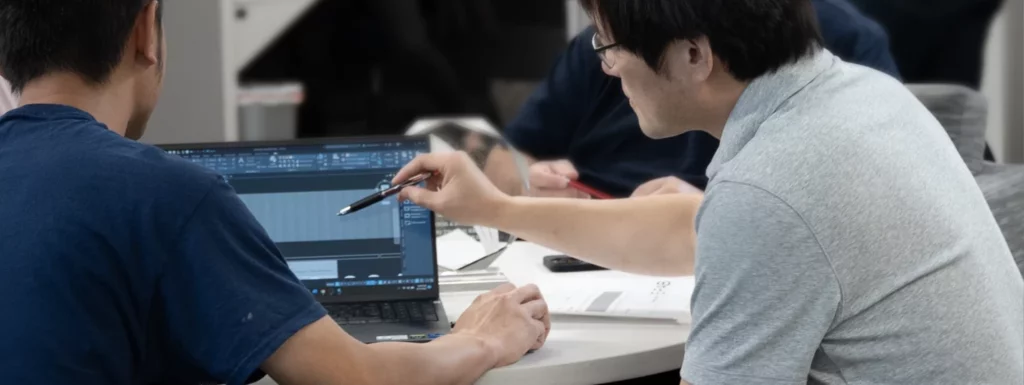
Why DFM Matters: Benefits and Advantages
DFM minimizes production costs by simplifying manufacturing processes and reducing the quantity of complex or custom-made components. It decreases material waste by maximizing material usage during manufacturing for peak efficiency. DFM also reduces the need for manual adjustments and fine-tuning during production.
The streamlined production process leads to shorter lead times from design to market. TPC manufacturing centers can respond more quickly to rapidly shifting market demands, and this is important at a time when globalization has added additional and different design and scheduling needs.
On the product side, DFM enhances quality, reliability, and performance and reduces manufacturing errors and defects across production runs. It also cuts back on waste, energy consumption, and environmental impact. TPC strives to be as green-friendly as possible and invests to ensure our manufacturing centers are sustainable and eco-responsible.
Integrating DFM into TPC’s Manufacturing Expertise
The DFM approach allows TPC manufacturing centers to offer a one-stop experience. Their mastery extends to niche processes like photochemical etching, ceramic metalization, crystal growth, and electropolishing. TPC recognizes the critical importance of DFM as a core principle across their operations, which ensures that products are not only innovative but also practical to produce. This approach minimizes production costs, accelerates time-to-market, and enhances product quality.
Here are two key examples:
Elcon Precision follows a well-developed DFM practice to evaluate and test its control grid design at the prototyping stage. Starting early ensures that Elcon’s manufacturing teams can consistently produce the part or component to the required specifications during production runs.
At Fotofab, DFM optimizes its photochemical etching process to provide its customers with superior cost-effectiveness, reliability, and high-quality parts. DFM achieves that by standardizing parts and reducing inventory; simplifying product design and minimizing the assembly process; resolving assembly issues with modular upgrades; reducing setup times and the number of operations to improve tools, workstations, and workflows; and remedying influences that impact product manufacturing such as the nature of raw material.
Another benefit to the DFM method is that it allows for reasonable and affordable alternatives to more pricey materials without sacrificing quality.
DFM Enhances Production Flexibility and Quality Control
DFM benefits TPC’s centers and customers alike during manufacturing runs since it is easier to institute design revisions and updates without major disruptions in production. Plus, DFM enables quicker changes in manufacturing techniques, technologies, and materials, which reduces disruptions and costs. Also, because more attention is paid throughout, the quality assurance process is smoother, with fewer rejected parts.
Our experience shows the benefits of DFM extend to the part application process — parts have increased adaptability and flexibility — and in the field — parts and components delivered are easier to maintain and service, which lessens downtime and repair costs.
DFM is Essential to TPC’s Productivity and Success
The DFM concept is a boon to every TPC client and manufacturing center and its different types of manufacturing.
E-Fab has noted that DFM is pivotal for business because it involves thoughtful consideration of materials, part geometry, tolerances, and surface finishes to ensure seamless integration with manufacturing processes.
But there are more general principles that extend beyond the TPC family: Streamlining production workflows, enhancing product quality, reducing manufacturing costs and improving profits, and accelerating time-to-market.
We look forward to sharing our experience and expertise. Please reach out if we can answer any questions or learn more about our manufacturing centers.